How important is it to have the right data on your wire and cable products? For those seeking qualification to a product standard, having test data that matches the requirements is important. Without this data, qualification cannot happen. But what about the products that fall outside of industry standards? How many tests are necessary to prove performance and product airworthiness?
Several past articles directly covered the physical, functional, and maintenance test factors that should be considered. Left out from these articles was how far a wire/cable assessment should go.
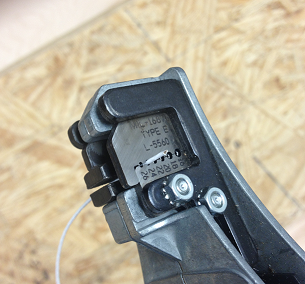
Basic Wire
A good basis for any basic wire for aerospace applications is the AS22759. Wires based on this standard are among the most common wires use in aerospace (many OEMs have general airframe wire that closely mirror this standard). Because of its wide adoption, this standard and the slash sheets (the configurations of wire gauge, conductor plating, and insulation type) cover a wide range of applications in aircraft environments. The following table provides a summary of performance ranges for the more modern constructions in the AS22759.
Property |
Value |
N/A or specified across operational temperature spectrum |
|
N/A or < 10 wires fail post test examination |
|
2.5kV |
|
Gauge Dependent (> 25lbs for 20AWG at 23C) |
|
Self-Extinguish: < 3s
|
|
Subject to more than 20 aerospace fluids without swelling or cracking |
|
N/A or 2000 hours (or more) at 70C |
|
15-day humidity cycling without Insulation Resistance change |
|
None |
|
24AWG – 10AWG: 5GOhm for 1000ft
|
|
Rated to -65C |
|
150 – 260 C |
|
N/A or no propagation of notch to conductor after bending. |
|
< 1% after exposure to elevated temperatures |
|
Conductor dependent |
|
26AWG-20AWG: 0.25 – 6lbs
|
|
Gauge dependent |
The aerospace industry is set up such that each generation of components is more reliable than the last. Because of this, it is very difficult to justify ignoring any of these tests or accept performance reduction in any of these categories. The latest generation of wires/cables have served the industry well and regressing in performance is difficult.
However, there are plenty of unique wiring applications on aircraft and, so long as the performance decrease can be justified, and it can be established that it will not have an impact on overall aircraft reliability, the component will be acceptable.
Cabling
To go beyond a single wire ran into a cable construction, there are two standards which provide a robust framework: NEMA25700 and AS6070. Those seeking guidance on general cable parameters should review Lectromec’s articles on AS27500. While AS27500 does provide a robust framework in which more than 1 million combinations exist, the test outlined in AS27500 does not provide sufficient guidance for those looking to evaluate the performance of a high-speed data cable; this falls into the AS6070 framework.
The AS6070 is a relatively new standard and the range of performance criteria is much smaller than that of the AS22759 wires. As of today (April 2018), only a few specification sheets have been identified. However, this is an ongoing effort and additional cable varieties are anticipated in the coming years.
The important elements to identify is that the AS6070 specification does provide guidance and recommendations on which methods should be used when evaluating high-speed data cables. These methods include velocity of propagation, surface transfer impedance, cross talk etc.
Conclusion
With all of the production variables and must be controlled, building a reliable, high-quality wire for aerospace applications is a true achievement. But without supporting data the claims are unsubstantiated, and the wire cannot be placed on the certified aircraft. Nothing is worse than a great product that cannot get to market.
To get past these roadblocks, Lectromec helps wire/cable producers prove the quality and performance of their products. With the capacity to perform 98% of all aerospace wire and cable tests in-house, you get the test data you need.