As EWIS (Electrical Wiring Interconnection System) engineering is becoming a more mature field, additional standards and requirements are being developed. The latest of these EWIS design standards is the IPC-D-620, “Design and Critical Process Requirements for Cable and Wiring Harnesses.” This pending standard, coupled with the design requirements of IPC (Institute of Printed Circuits) documents, IPC/WHMA-A-620, IPC/WHMA-A-620(Space), IPC/WHMA-A-620A, specifies general design and critical process requirements for EWIS harnesses and cable assemblies. The targeted reader of the document is a design engineer, manufacturing engineer, or quality engineer. However, many of the design philosophies and quality assurance requirements can prove to be useful for anyone working with EWIS. We will review the document in this article as well as an upcoming article.
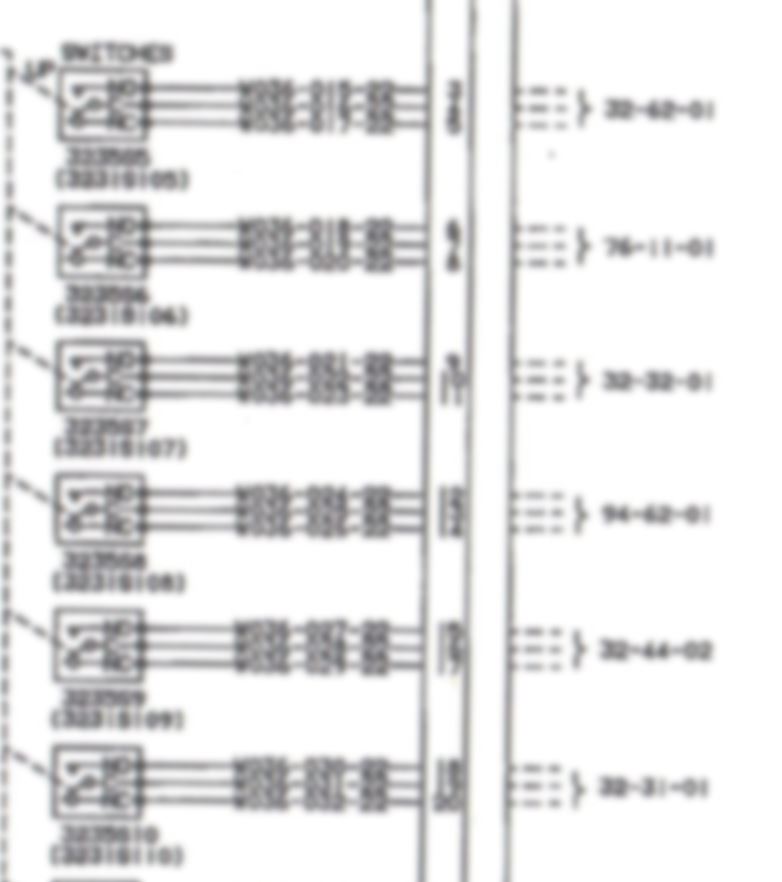
Overview
IPC-D-620 covers design requirements, quality assurance requirements, assembly/fabrication requirements, electrical requirements, and parts, materials, and processes requirements. Each section has multiple subsections that cover a wide range of specifications related to each topic. Each topic thoroughly covers each area and includes references to other documents that provide additional information and resources. Overall, IPC-D-620 recognizes that wiring assemblies are subject to different classifications based on the end product and it does an excellent job at identifying and explaining general requirements.
Design Requirements
Those familiar with EWIS regulatory requirements will recognize the importance IPC-D-620 places on thorough EWIS analysis. Such an essential component requires good design and requirements from the beginning so as to not compromise the aircraft. Since the EWIS is such a critical system, the design of wiring harnesses should be based on the worst-case requirements and scenarios. This would ensure that EWIS will not fail in the worst situations and keep the vehicle running long enough to avoid a Class A Failure (loss of life or aircraft).
IPC-D-620 details basic design considerations for design engineers to review in order to ensure reliable cable and wire assemblies (this provides some guidance that goes beyond the recommendations found in existing installation standards such as AS50881). The main items for consideration are the wire and cable harnesses’ physical and material properties. Weight, tensile strength, current and voltage rating, resistance to cold/heat, flammability, and stability are a few of the primary properties that must be considered in the vehicle’s wiring system design. Other basic design considerations include application usage, the quality of non-metallic components, environmental regulations, and special handling requirements.
Not all wiring systems will experience the same conditions while in operation, so there are different requirements design engineers must follow depending on the end product. SWAMP (Severe Weather and Moisture Prone) area wires will need to adhere to different requirements than wires near the heat sinks since they will be exposed to very different environments throughout the service life. IPC-D-620 does not specify requirements for multiple environmental conditions and instead references documents that have that information in much more detail. IPC-D-620 does, however, have installation/design reminders such as providing slack when necessary and avoiding damage from fumes and fluids.
An area that is lacking cohesiveness is information for different situations; like most standards, the information is spread across dozens of references. However, IPC-D-620 was meant to be a general document and provide information such that it can be applied to the broad spectrum of wiring harnesses. Interested readers should read Lectromec’s Aerospace Wire Inspection? Time Tested Guidelines article for more information on wiring systems in different environments.
Quality Assurance Requirements
Including quality assurance guidelines from the beginning ensures that the wiring system will need less intense maintenance and will make the aircraft stay operational for a longer period of time. Quality assurance is crucial to making sure that standards and procedures are followed properly and any problems are fixed before deployment.
IPC-D-620 states that the supplier (harness manufacturer) is responsible for testing the wires before shipping them out to be used. For those seeking to follow this emerging standard, they need to follow all tests and inspections laid out in IPC/WHMA-A-620 and IPC/WHMA-A-620 (SPACE), which include qualification tests, acceptance tests, physical configuration tests, and parts, materials, and controls tests. The document does not provide significant detail on quality assurance. This would likely fold into a manufacturer’s existing quality control process.