Key Takeaways
- Shielding on aerospace cables offers several benefits but can introduce some drawbacks that must be considered.
- A Cable shielding’s primary purpose is to limit the impact of radiated energy on the cable itself or other nearby systems, making it essential to consider for modern-day high-voltage (HV) aircraft.
- Cable shielding negatively affects the weight, flexibility, physical complexity, and diameter of a cable all of which may impact EWIS design and installation.
The high electrical power needs of aircraft have resulted in the design, development, and testing of a wide range of new components. While many of the EWIS design patterns remain the same, changes in EMI sensitivity of electrical equipment have also pushed changes in where and how EWIS is deployed in the aircraft. One of the most common tradeoffs EWIS engineers must undertake is the extent of shielded is used in the EWIS. Lectromec has touched on this topic before, but this article specifically considers the needs of all electrical hybrid aircraft high-voltage power feeder cables and the use of cable shielding.
Background
A Cable shielding’s primary purpose is to limit the impact of radiated energy on the cable itself or other nearby systems. Traditional aircraft design has been to select unshielded cables for the power feeders and shield only those cables connected to sensitive circuits. This limited the shielding to smaller cables usually with conductors sized 20 – 26 AWG.
With different system needs and performance requirements, the EWIS design patterns have needed reassessment to achieve optimal design and reassess generally accepted assumptions on balancing performance with conservative design techniques. The following are several high-level factors for and against using shielded high-voltage power cables.
Pros
The consideration of shielding for HV cables is for the following reasons:
Magnetic field protection: Depending on the location of the cable routing in the aircraft (if it is high powered and near crew or passengers) health concerns may exist. Cable shielding helps to reduce the magnetic field strength thus reducing the potential health concerns.
Switching: Depending on the power system configuration, the EMC (Electromagnetic Compatibility) impact of the high-voltage DC distribution system might be minimal, but once converted to alternating current for the propulsion system, the high-frequency switching of the power can be a major source of EMI (Electromagnetic Interference). How the switching system is designed will also impact the generated EMI. A shielded cable, braided or foil-wrapped, can help to reduce this impact
Separation Distance: The addition of cable shielding may help to reduce the required separation distance between the power and signal cables. This can be in two ways: EMI protection and arc damage. From an arc damage perspective, a cable shield can either act to support the continuation of the arcing event (if electrically connected to the power system through a common ground) or help to slow the progression of the arcing event. If not electrically connected, the shield is a layer of metal that must either be damaged or destroyed by the arc’s thermal energy; this is a significantly less effective method for metal destruction than direct electrical arcing. It is because of this that the shield can act as a barrier and help to reduce separation distances.
Fault detection: Adding a shield to the cable provides a means to detect if there is a fault in the high-voltage wire insulation. This might be a direct shorting event to the shield (likely near a termination point) or, for high-sensitivity systems, this could also be a mechanism for partial discharge detection. The capability to detect and isolate these types of faults does not remove the additional burden of sensors and monitoring equipment, but as the high-voltage parts of EWIS evolve, this could become a critical part of a health and monitoring system. In particular, this could be part of flight testing of new platforms that do not have the historical data to determine part longevity.
Additional Protection Layer: The shielding also means that there will likely be a jacket on the cable. Given the potential impact of a high-voltage wire fault, it is beneficial to have additional physical barriers to limit damage. From a scrape abrasion and notch cut perspective, adding a jacket and shield can dramatically increase the protection from mechanical damage.
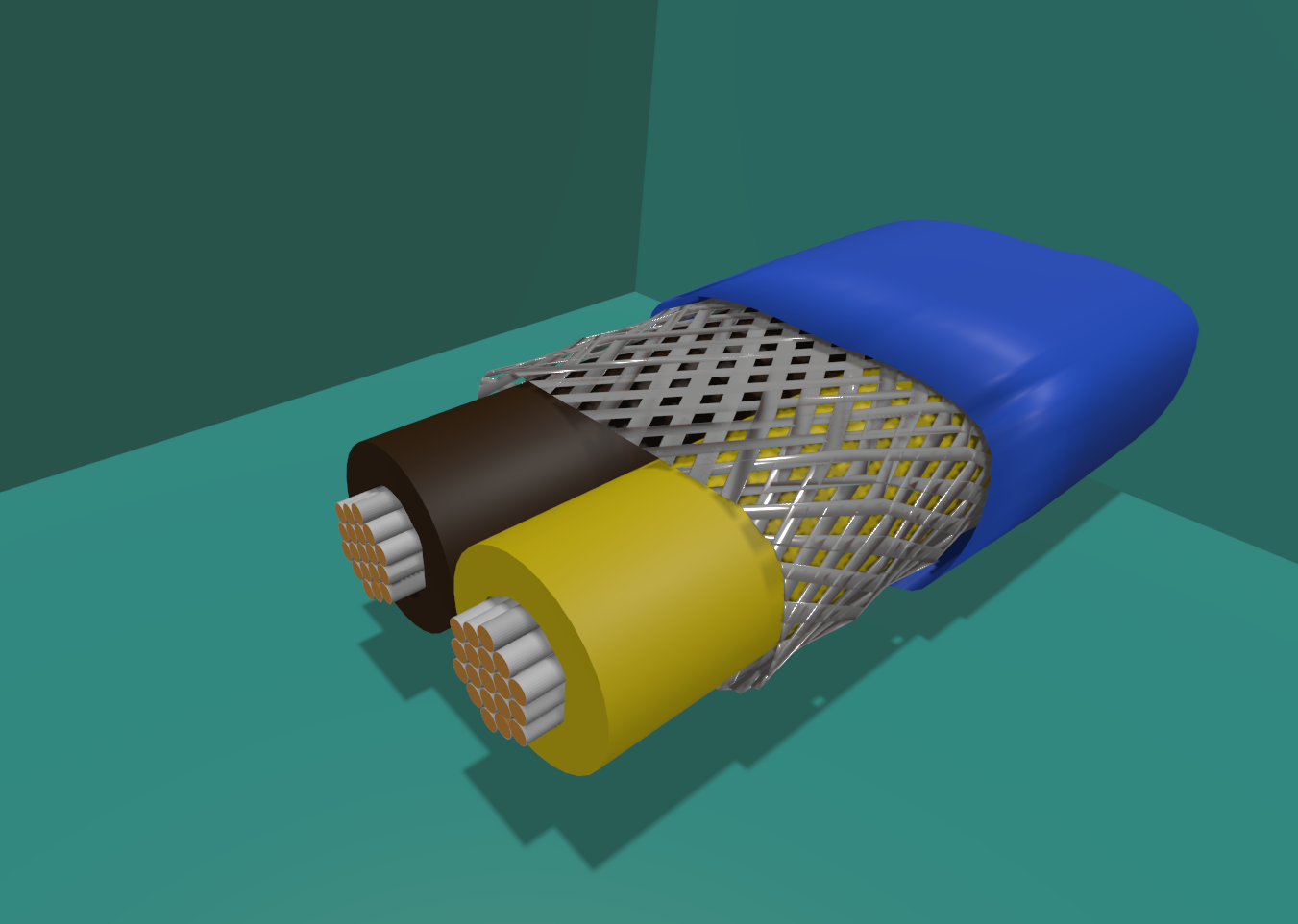
Cons
The use of shielding does have disadvantages that should not be ignored.
Cost: The additional cost of cable shielding is not insignificant and should be considered as part of the engineering tradeoffs for use. The optical coverage, type of shielding, and design (round conductors versus flat conductors) all have an impact and need evaluation.
Flexibility: Shielded cables increase the resistance to mechanical flexing. Even under ideal designs with small gauge, high strand count shielding, a shielded cable requires more force to bend than a non-shielded wire. This impacts the product’s workability as well as performance in flexing applications.
Weight: In the aerospace industry, additional weight is often viewed as the greatest negative for any product. Shielding does add weight to any cable and the amount of extra weight is based on several factors including cable size, coverage, type of conductor used for shielding, etc.. Using that as a starting point, if there is not a justification for the use of a shielded cable (and the arguments for shielding earlier in the article were not persuasive enough), then the additional shielding weight should be sufficient reason to avoid the use of the cable shielding.
Diameter: The addition of cable shielding and jacketing does not add too much to the cable diameter, but if there are tight spaces in the aircraft (feedthroughs, conduits, etc.) where space is limited, the additional cable diameter is noticed.
Maintainability: Shielded cables take more effort and more tooling to repair. When considering high-voltage cable repair, this also requires that all of the components used for the repair are rated for high-voltage use and can provide the same performance and protection as the original part.
Ground Plane for PD (Partial Discharge): If the cable shield is connected to the electrical circuit (typically as a ground), then there is a voltage gradient across the wire insulation that provides potential locations for partial discharge. Without a shield, the opportunities for PD from the HV wire become more limited. Of course, by selecting a cable with a high PDIV/PDEV across the entire operational profile of the vehicle, PD can be avoided in most cases.
Conclusion
EWIS design is no longer as simple as picking a qualified wire/cable and installing it anywhere in the aircraft; the performance requirements of high-voltage aircraft now require greater attention to detail. The pros of using a shielded high-voltage cable should provide sufficient justification in many cases for their use and should probably be the default for most applications. With shielded high-voltage cables as the default, an analysis must then be done to justify using un-shielded high-voltage cables; the expectation is the analysis will go beyond a simple statement of “because it weighs less” and more deeply consider the aircraft level impacts.
If you are looking for support for your high-voltage EWIS analysis, testing, or certification, contact Lectromec. We have been supporting high-voltage EWIS development when it was still in the fundamental research stage and can help you with your current development needs.