Key Takeaways
- Wire and cable insulation degradation has been a field of active research for decades.
- The degradation research makes it possible to predict the remaining reliable service life of aircraft wiring systems.
- This technology has been used in dozens of projects to provide a data-backed solution for wiring system sustainment and replacement planning.
We can look at a banana and, with a high degree of confidence, guess at a banana’s firmness and taste. This is possible because we have been exposed to bananas throughout their life cycle and know what the colors and spots mean. With bananas, we can look at them and have a fairly decent prediction as to how long it will be before they should be discarded and are no longer edible.
Unfortunately, the aging of wires and cables is not like a banana. We cannot simply look at a wire/cable and identify its current condition or the remaining reliable service life. It is a more involved process to identify a wire/cable’s condition.
To understand the basis for wire life prediction, there are parts of the process that must be understood from a fundamental perspective and how these fundamentals are applied to the long-term reliability and life prediction of the components. This article will cover some of these basics, the research that has gone into this field, and how it is used as part of EWIS sustainment and service life extension projects.
Background
Wires and cables are comprised of two parts: the insulation and the conductor. For the aerospace wire/cable insulation, this is often a fluoropolymer. These polymers are made up of long chains of monomers. When the insulation is new the molecular chains are long but as the insulation age was exposed to electrical, mechanical, thermal, and/or environmental stresses, the chains break and slowly reduces the insulation performance.
Research
Material degradation is not something that is solely isolated to the aerospace wire and cable insulation field. The materials that go into aerospace wires and cables are used for various purposes across multiple industries. As such, the performance of these materials and long-term stability is of critical importance for all the applications they support. Where this becomes a bit of a more complicated issue, is that some of the formulations that are used for aerospace can vary from other applications. Specifically, there are additives to some insulation products to ensure good performance (such as for flammability or mechanical strength) that is needed for aerospace wires and cables. These additives do change the material performance and, in some cases, change the degradation modes.
Research into wire insulation degradation has been going on for decades. Among the first activities undertaken by Lectromec back in 1984, was the investigation into polyimide insulation degradation. This research investigated several means of determining the material degradation and ways to predict future performance. After years of study, two technologies developed by Lectromec and industry emerged. The first technology was Lectromec’s WIDAS (wire insulation degradation analysis system), the second technology was inherent viscosity (both used by Lectromec today). These two technologies are a means for assessment and achieve the same goal: identify the current condition of polyimide wire and use the data gathered from physical testing to predict the remaining reliable service life.
This research was expanded upon in the late 1980s and 1990s as both commercial and military organizations started to see the need for a means of identifying wire system health. Several research efforts were undertaken by the U.S. Navy, U.S. Air Force, the FAA, NASA, and commercial organizations (including Lectromec). As the number of both parties increased so did the scope of wire degradation assessment. Investigations were beyond the polyimide wire constructions to include other wire types that were commonly found on aircraft to include ETFE, polyalkene Kynar, XL-ETFE, and composite constructions (PTFE-PI). It is now possible to predict the remaining service life of most aerospace wires and cables.
Life Prediction
The research outputs sought to answer the following:
- Is it possible to ascertain the current health of wiring on aircraft?
- Is it possible to identify a key property that can be used to limit the service life on the vehicle?
- And lastly, is it possible to predict how long it would take to go from the current condition to the end of service life?
In effect, the objective was to develop a predictive tool for the following:
- Identify those wire harnesses, systems, locations within an aircraft that are in most need of focused maintenance
- Identify those wire harnesses, systems, locations within the aircraft where wire harness replacement is needed
- Reduce the number of wire system failures by proactively addressing EWIS issues
The accompanying figure shows the application of just such an idea. In this, a wire or cable has initial performance value that has been established through other testing. Some samples have been removed from the vehicle and physical, electrical, and/or mechanical testing has been performed to gather data about the current health. Using information about the current condition and when the wire/cable was installed on the vehicle combined with the degradation models, it is possible to predict when that minimum threshold is surpassed.
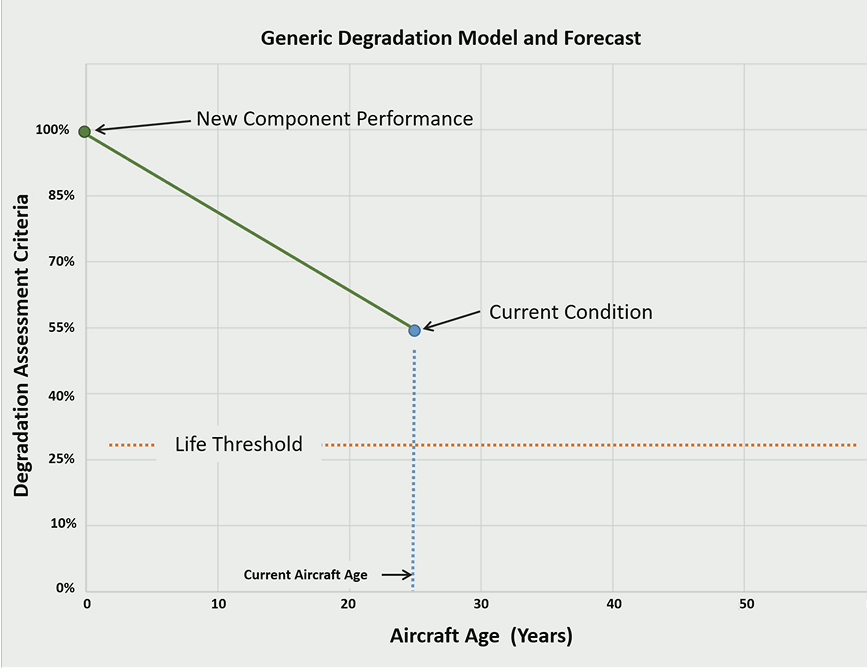
By identifying the current health and the remaining reliable service life, maintenance actions can be better scheduled and focused on those areas most in need. Coupling the degradation information with maintenance data, as discussed in the previous article, makes it possible to support EWIS sustainment efforts. In particular, this makes it possible for data-supported decisions to be made, and not just use anecdotal evidence for maintenance actions.
Actual implementation
This is a field that Lectromec has been working on for decades (white paper available here). We have had the opportunity to deploy this technology on several fleets across the globe to:
- Focus the EWIS maintenance actions
- Identify those systems, wire harnesses, zones most in need of replacement
- Avoid costly replacement of good-quality/good-condition wiring.
While there are some cases where a full aircraft rewire can be beneficial, Lectromec has never come across an aircraft fleet where a full rewire is needed based upon wire system degradation. This has made it possible to focus attention and funding to more critical tasks of EWIS sustainment. And the cost avoidance is not a trivial amount; one small fleet saved more than $50 million following Lectromec’s EWIS condition assessment.
Conclusion
In the last decade, the aerospace industry had moved beyond assigning the EWIS (electrical wiring interconnection system) as a “fit and forget system.” Regulations have pushed the level of care and assessment to a new level. Thankfully, research has been conducted to develop assessment technologies to support the identification of wiring system health. This makes it possible to not only take care of a wiring system but to take care of a wiring system in the most time-efficient way possible to maintain aircraft airworthiness.