We measure everything that matters. In the last decade, the efforts of organizations to measure EWIS has been progressively increasing. Perhaps this is because wiring is now considered a system, or because regulations and requirements have emerged, or it may be due to a better understanding of the EWIS maintenance costs. Whatever the reason for better EWIS maintenance issue quantification, it has been a positive because there is data available to substantiate aircraft maintenance actions. The old saying is, “You can’t beat something with nothing”, and for too many years, EWIS maintainers were trying to take on EWIS maintenance without supporting data.
Improve the Capture
For those organizations that have not taken on quantifying their EWIS health, it is important to measure its current condition, and in particular capture the EWIS failure and maintenance data. Within the USAF, the review of EWIS maintenance data has been hobbled because maintenance actions could not be assigned an EWIS specific work unit code (WUC) associated with EWIS (the commercial segment has been able to adapt more quickly). Where the EWIS related failures and maintenance cannot be separated, EWIS failures would get lumped in with other systems and this would require a need for a significant amount of effort to extract information and make it usable fractions.
Thankfully, the latest revision of MIL-DTL-38769 (Rev G) has included a work unit code for EWIS. While this does not solve the historical data challenges that are still present in many fleet systems, implementing a separate work unit code or maintenance action code related to EWIS can help future data evaluation.
Getting the Data
At a high level, the process for EWIS failure and maintenance data collection should include the following tasks:
- identify all the repositories where EWIS data may be stored
- gather the data into a single location for review
- filter the data to remove non-EWIS related events
- partition the data in such a way that it can be used for EWIS data analysis
When expressed at a high level, the task seems relatively simple and almost uninteresting. However, those who have dealt with maintenance data know that the first two steps are relatively easy, and the third step is where the complexity and the burden of the work takes over and often hinders efforts.
Thankfully, some of the processes for the data analysis are captured and discussed in the US military handbook MIL-HDBK-525. While a manual intervention is required for some parts of the data capture, knowledgeable use of filtering and queries of the data can help to reduce the overall manual labor associated with the task. As part of Lectromec’s work to review maintenance data, we have developed advanced algorithms and analysis techniques that have helped to identify and extract EWIS maintenance actions from raw maintenance data with a very high degree of accuracy. As an example of this, Lectromec used the raw data gathered and manually sorted for our white paper on EWIS failure rates [link]. The algorithm was able to accurately identify EWIS maintenance action more than 80% of the time (we will be using this to update the white paper in the next couple of months).
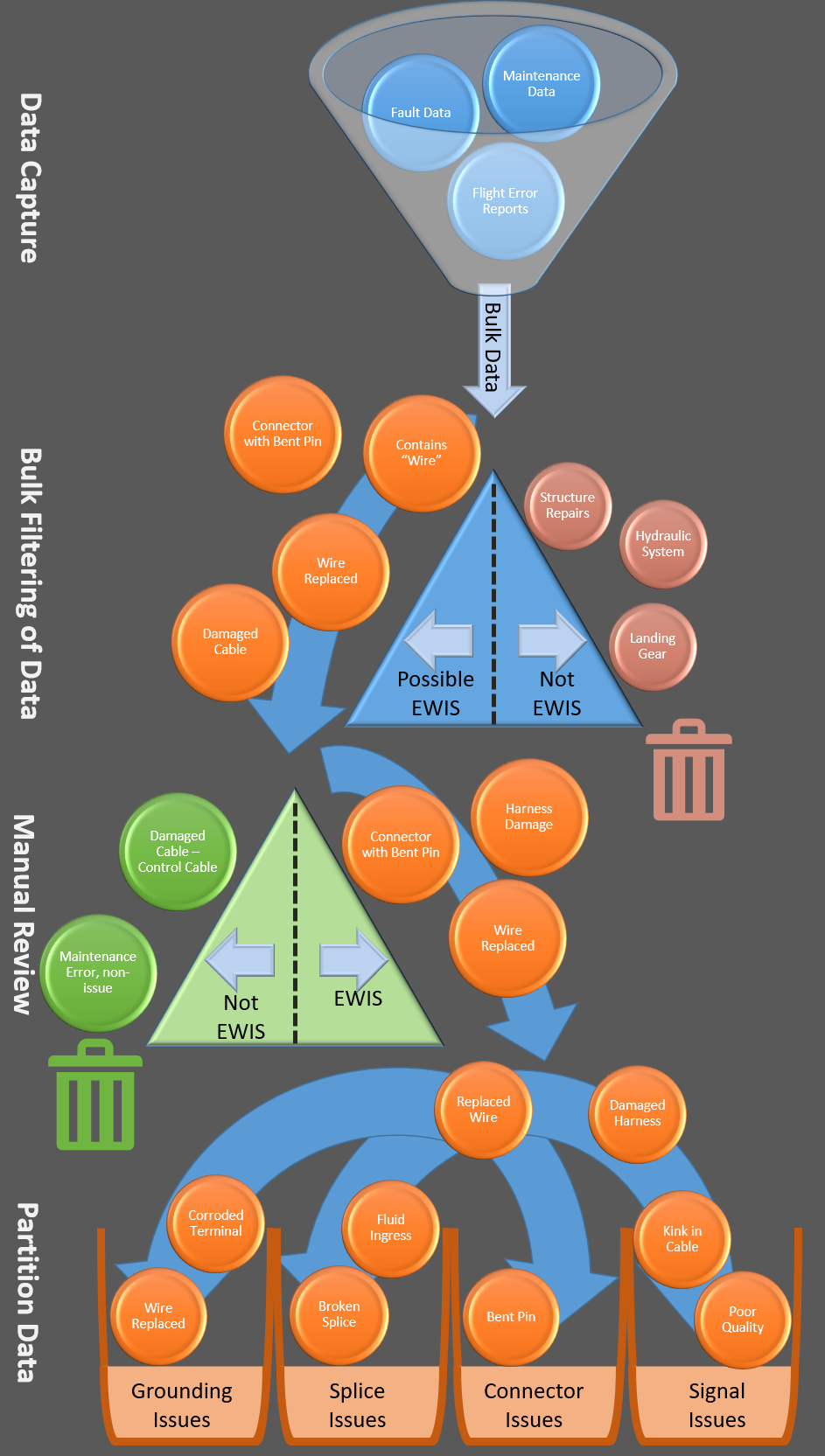
Evaluation
For some, the bulk of the work and the major complexity with this effort is with the data capture. After this, the data analysis is mostly straightforward and similar to other processes used for data evaluation. This includes:
- Hotspot analysis: Identify common areas of failure on the aircraft.
- Trend analysis: A review of failures over a defined period to determine if there is a progressive increase. Often Weibull analysis is a means to review the data.
- Pareto analysis: This suggests that 80% of the problems come from 20% of the systems or locations within the aircraft. Often this can be used to “get the biggest bang for the buck” by focusing on the few systems/locations where most of the improvements must be made.
These do provide a good point for starting EWIS sustainment and provides a good understanding of the current EWIS health. Trend analysis is inherently based on historic data and the extrapolation of that data can only go so far. For those that wish to get the most from their fleet sustainment activities and the biggest return on investment, there is another step that should be taken (there is a reason data evaluation is Task #2 of 7 in the MIL-HDBK-525).
Data to Support Testing
To get an understanding of the degradation of future EWIS health requires selective sampling and testing of EWIS. This technique has been employed across dozens of fleets to:
- Plan for upcoming maintenance activities
- Capture the actual risk posed by the EWIS
- Improve fleet readiness and available operational time.
An example of this is shown in the accompanying figure. Directing tests to specific areas for focused degradation testing yields the most value to fleets.
Wrapping it up
Reviewing maintenance data is a non-trivial task and it yields non-trivial value to the fleet maintenance. By identifying the maintenance actions taken on an aircraft’s EWIS, it is possible to assign the cost of EWIS issues, not just of the activity itself, but the impact the failure had on aircraft operations (e.g. emergency landing, aborted takeoff). It is by measuring the EWIS performance that actions make sense and can drive the necessary, potentially proactive, maintenance. After all, there is no reason to take action (proactive or otherwise) unless there is data to support it.