Key Takeaways
- Notch testing examines the impact of a small cut on a wire.
- Methods vary on the wire/cable performance assessment but relay on three parts: cut the wire insulation, mechanical stressing, and assessing the cut site.
- The notch test is a good way to screen wires/cables and identify their susceptibility to damage.
How much damage can a single wire take? Does the failure of a wire’s insulation require one large trauma (think of dropping a hammer on it), or is it possible for the insulation to fail due to 1,000 small cuts? That has been a question plaguing wire system sustainment for decades. Identifying one large trauma can be easy, but to catalog all the minor traumas is impossible.
There is at least a means to determine if a wire’s insulation can withstand at least one cut. The means to do this is with the notch propagation test.
Test overview
In this test, a razor blade is set in a test fixture such that only 1 – 5 mils (0.0254 – 0.127 mm) of the blade is above the fixture. This limits the penetration to the blade height.
The blade is then run across the wire (perpendicular to the wire length) to create the notch in the wire insulation. After the cut is made, the wire is then subjected to a bend test in which the wire is wrapped around a mandrel. This wrapping action is indented to mechanically stress the insulation, and the notch location, such that the notch expands and potentially propagates to the wire conductor.
Test Method
The most common standards for aerospace notch propagation are the AS4373 and the EN3475. At the core, they both seek to apply a notch; the two standards differ in what happens after the notch is created.
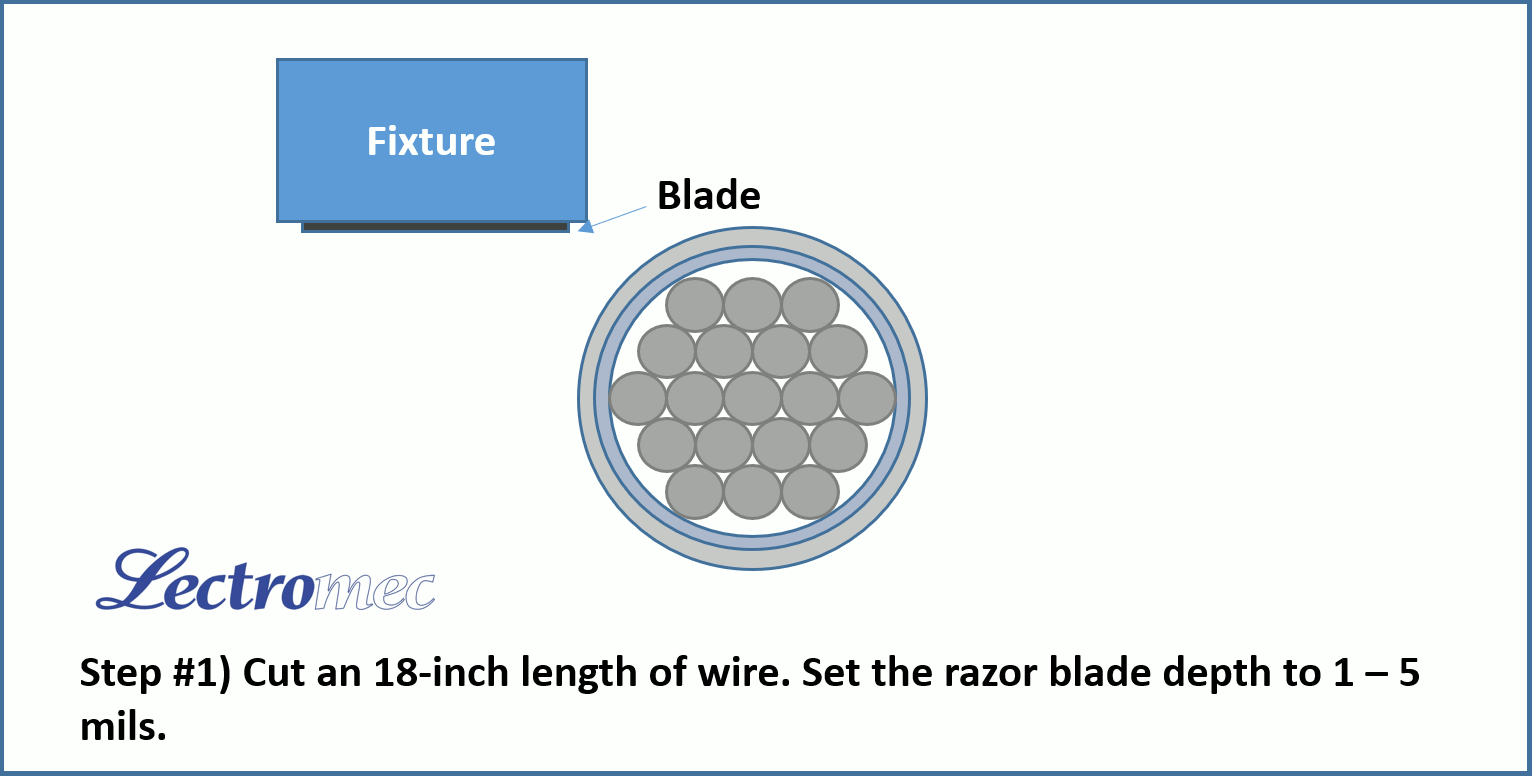
In the AS4373 test procedure, the post-notch wrapping and unwrapping continue until either the conductor is exposed, or 100 cycles have been completed (whichever is first). If the specimen passes the 100 wrap cycles, it is again visually examined for an exposed conductor. A specimen has passed the test if no conductor is exposed.
In the EN3475 test procedure, the post-notch wrapping is done only once, but the sample is then subjected to a wet dielectric test.
Both test methods have merit in the test performance. The AS4373 method examines the case where the wire/cable is in a flex application or if near a disconnect. The EN3473 method considers a common case of stationary wire and dielectric breakdown with the application of voltage. The selection of the test method should be done to best reflect the application.
Tests on Cables
This test may also be performed on cables. When this is done, the same procedures are followed except the objective is to determine if there is a breach of the jacket to the cable shield. The same pass/fail criteria used for wires may be used for cables.
In Application
In application, the notch propagation test would eliminate any aerospace wire construction that is identified as ‘lightweight’. Lightweight wire constructions (such as AS22759/91) have a wall thickness minimum of 5.8 mils. While it is possible that a 5 mil cut would not cut through to the conductor, it is likely that a breach would propagate during the bend test or a hole would be created when voltage is applied in the dielectric test.
Organizations that place value on the notch propagation test will often mitigate the risk of insulation damage by either
- Requiring all lightweight wires be in wire harnesses with additional sleeving/protection, or
- Require lightweight wires to be in a jacketed cable.
[Side Note: naturally, the value of lightweight constructions often comes up when factoring in additional protection requirements. This will be addressed in a future Lectromec article].
By adding this additional layer of protection, the wires are protected from small cuts.
Conclusion
The notch propagation test is one of many tests to evaluate a wire/cable’s insulation performance. By creating a little insulation damage then mechanically stressing the wire, it is possible to see if the insulation is likely to tear after a small cut. The test itself is straight forward, but the application of the results is not. The results are pass/fail, so it does not provide much information when comparing different wire/cable constructions. A means to augment the test is to progressively increase the blade penetration to see when the sample fails. In doing so, additional value can be gained from the testing.
As always, Lectromec’s ISO 17025 accredited lab is available to perform this or any other wire/cable test you need. Contact us to find out how we can help your wire/cable test project.